Proto-Form Vacuum Forming Machine Plans
Create and mold complex plastic shapes by using heat and vacuum!
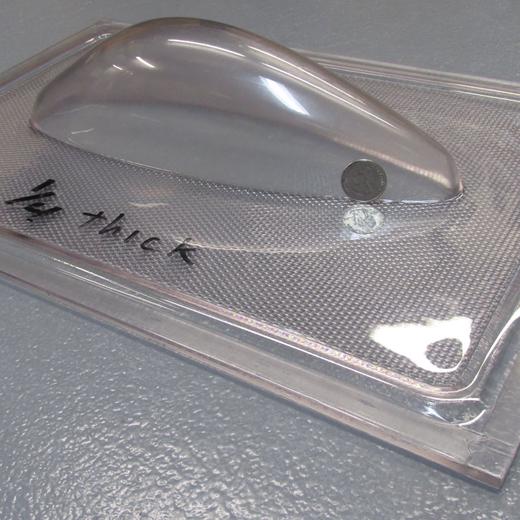
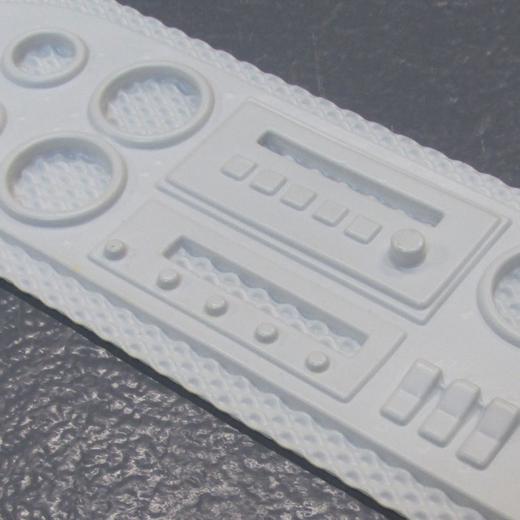
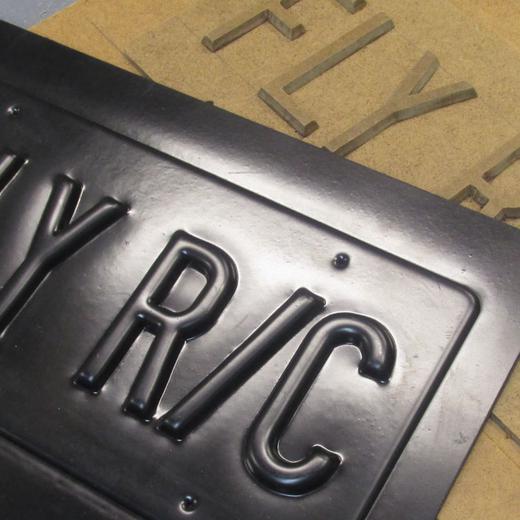
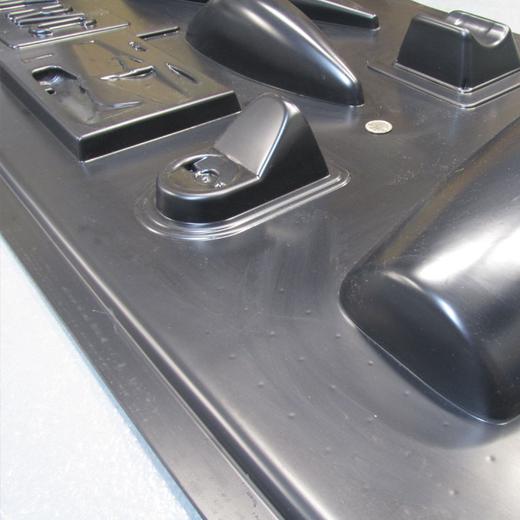
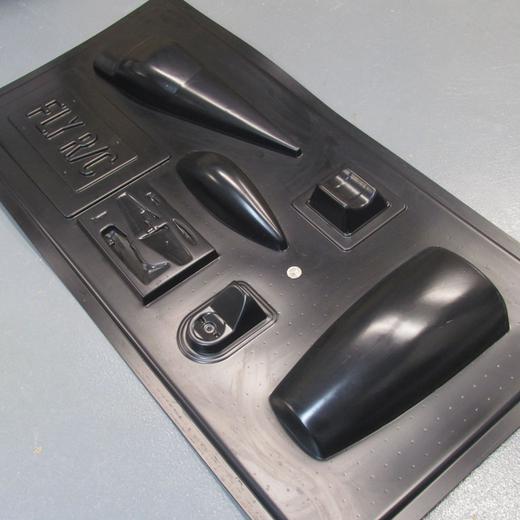
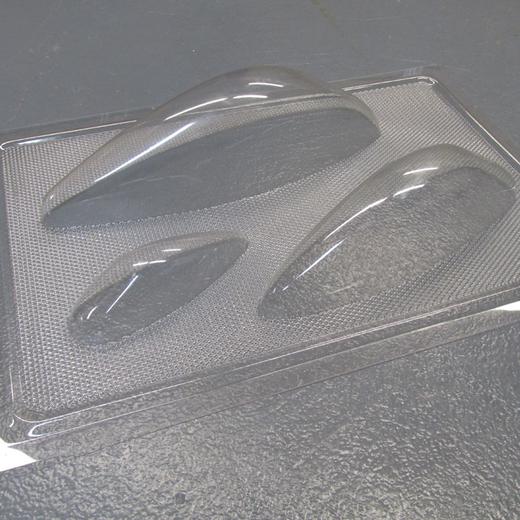
What can it do?
“Vacuum Forming” or “Thermoforming” is a simple process where you take a flat plastic sheet, and heat it until it’s soft. Then you stretch it over a mold or pattern, and suck it down tightly with vacuum. The plastic cools quickly and retains that shape. Vacuum forming is ideal whenever you need a “shell” type plastic part with uniform wall thickness. You can form over wood, plaster and many other materials. (See sample parts below)
Your Vacuum Forming overview, parts lists, building instructions, then “how to operate” instructions were well beyond the promised blueprints.
Kevin and Michael Ford
How does it work?
The typical cycle time ranges from 1 to 5 minutes depending on plastic thickness. Form up to 1/4 inch thick sheets!
Lets go through the process:
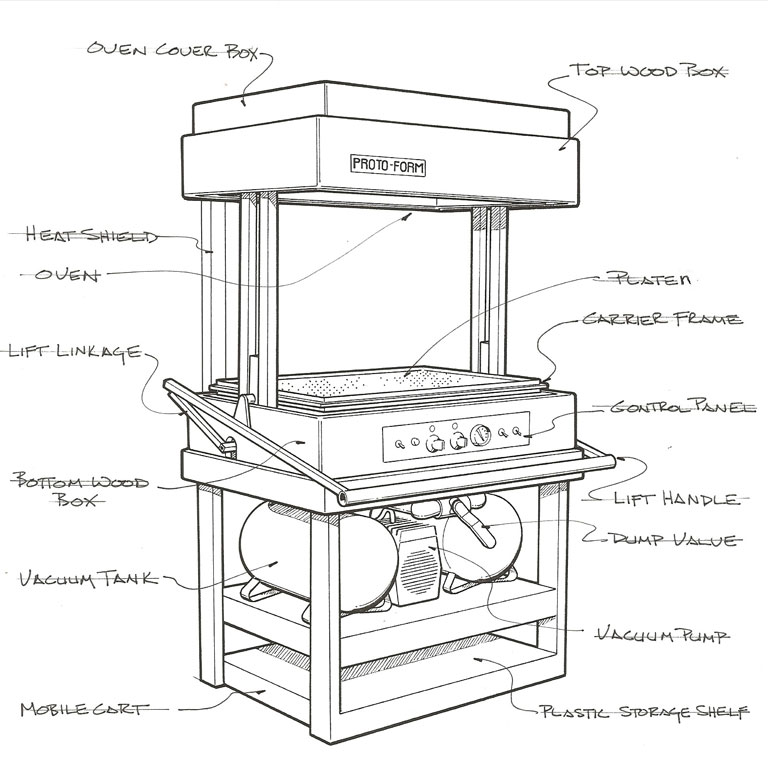
- Clip a plastic sheet into the carrier frame and raise the lift handle until it locks. This raises the plastic to the overhead oven where it will heat until it gets soft.
- Place your mold or pattern anywhere on the perforated forming surface below, (also called the platen). When the plastic has the correct amount of sag or droop, its ready to form.
- Lower the handle to bring the soft plastic down and stretch it over your mold. When the handle is all the way down, open the dump valve to release the stored vacuum and suck the plastic down tightly.
- The plastic cools quickly and the part can be removed.
- Load another sheet and do it again.
Who is it for?
Finally an affordable solution for the thousands of small businesses that need vacuum formed parts.
- Model Makers
- Maker Spaces
- Prop Designers
- Mythbusters
- Inventors
- Design Studios
- Theaters
- Specials Effects companies
- Cosplay
- Candy makers
- and more!
The Proto-Form machine is perfect for prototype parts and packaging, display models, signs and even volume production of high quality parts. Your machine will have identical performance to units costing $10,000+!
Now the alternative to those high priced machines is to build your own. The concept is very simple and the parts and materials don’t cost much. In addition to our comprehensive construction plans, we offer oven kits and vacuum pumps to make your project go smoothly.
Identical performance to units costing $10,000!
Free Bonus: All plans now include these two free supplements. Tips on enlarging your machine and how to add a two stage vacuum system!
Proto Form Specifications and Features
Small | Medium | Large | |
---|---|---|---|
Sheet size | 24 x 24 in. | 24 x 36 in. | 24 x 48 in. |
Platen size (usable area) | 21 x 21 in. | 21 x 33 in. | 21 x 45 in. |
Depth of draw | 12 in.+ | 12 in.+ | 12 in.+ |
Max plastic thickness | 1/4 in. thick | 1/4 in. thick | 1/4 in. thick |
Max vacuum (in H.G.) | 25 - 29 | 25 - 29 | 25 - 29 |
• High Output Oven
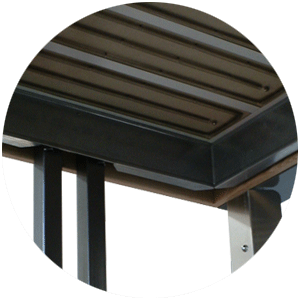
High output infrared design tuned to put out the correct wavelength for plastics to absorb. Don’t be fooled by the simple appearance and materials, this method of heater construction allows us to optimize a heater for specific applications such as this. Off the shelf “catalog” heating elements can only come close while costing much more. Not only is this oven design the cheapest, it provides better heating for plastics even while using less power than standard elements. You can spend more but you can’t do any better with commercial ovens!
• Heat controls and Zones
The oven can be split into zones (center and outer) if needed, but no controls are recommended. The watt density and wavelength is optimized and any adjustments will decrease performance.
• Vacuum System
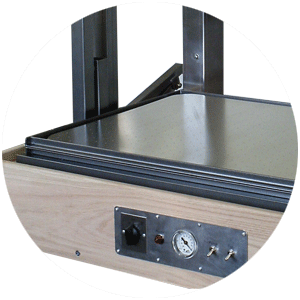
Plans show how to properly size the pumps, tanks and valves for each machine. Suggested combinations are given for budget or performance systems tailored to each size machine. Includes sources for low cost pumps and tanks.
• Clamp Frame
Simple, rugged manual lift system is hard to beat, its smooth fast and provides plenty of leverage. Simply raise the handle to heat the plastic and lower it when ready to form. Plans show cost effective way to hold plastic sheet with spring clips as well as quick release toggle clamps.
• Platen
Unique design uses an all metal air tight sandwich construction over a wood base.The ultra low internal volume means fast response, and zero leakage makes this a high performance machine. The platen is easily removable. Make as many different sizes as you need.
• Rugged Construction
The chassis is welded square steel tubing and the exterior panels are made from wood. No gaskets or seals to replace and no real wear parts means low maintenance. This machine is rugged, yet attractive enough for any design studio.
What’s in the plans
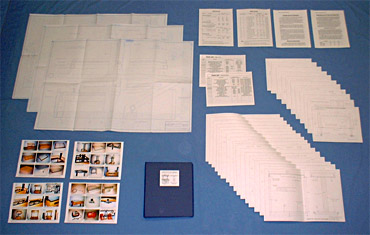
Proto Form plans when printed
This photo shows what the plans look like when printed out. You can take a disc or the PDF to Kinko’s and print the full set, or view it on your computer and print only what you need. The blue binder shown in the photo contains the 100 page illustrated assembly manual.
Again, you get all of this in the PDF. The photo just shows the large volume of information if you print it all out.
Complete specifications are given for all parts as well as part numbers from two large mail order companies. Save a lot of time, just call in your order and have your parts in a few days. Easy to read construction manual includes illustrations to make every step easy to understand.
An important chapter on planning clearly explains the options available to help you make the right choices, and discusses the skills and tools needed for building. If you will be hiring someone else to build all or part of your machine there is special information to help you find qualified sources.
10 chapters cover all details of construction. Helpful “Tips” throughout the manual, are filled with practical information on building, using and customizing each area. Options are offered wherever possible to let you make substitutions. Clear explanations, photos and diagrams will guide you through it. Not only will you learn how, but you will also learn why it works. Finally the section on operation will have you up and running fast with useful tips on troubleshooting common problems.
- 106 page illustrated assembly manual with wiring diagrams.
- Separate parts lists, wood and steel cut lists and pump and tank sources.
- 27 parts drawings
- 3 full size cut-away drawings
- 36 color pictures
- Written, detailed instructions that guide you through the build process
- Tips and techniques for the vacuum forming
Sample Parts

- The top part is a full size car fender made from 3/16 thick ABS.
- The part on the left shows the crisp definition possible even with 1/4 inch thick plastic (Styrene)
- The black part is .090 Styrene and shows some of the possible shapes you can vacuum form