Vacuum Forming for the Hobbyist PDF eBook digital download
Learn how to use heat and vacuum to mold flat plastic sheets into complex shapes. Build your own low cost equipment using hardware store items and your kitchen oven as a heat source.
This popular book takes a common manufacturing process and boils it down to its simplest form, so it can be done right in the home. It’s a mystery to me why vacuum forming is so largely ignored in the hobby and craft fields. It’s a fast and easy way to mold high quality plastic parts. Best of all, it requires no special skills and very little equipment.
This book goes beyond vacuum cleaners as a source of suction and shows you how to get 5 times more forming power. Chapter 2 tells why heat lamps and heat guns won’t work well, and shows how to use your kitchen oven and alternate heat sources
Chapter 1 - The Basics

Vacuum Forming (also called Thermoforming), is a simple process that uses heat to soften a plastic sheet, and then vacuum to suck it down tightly against a pattern or mold. The plastic quickly cools and retains this shape.
You can start with flat plastic sheets up to 1/4 inch thick and heat them in your kitchen oven. The mold or pattern can be made from wood, plaster, epoxy resin, aluminum, plastic and many other materials or built up from a combination of materials. Many times, you can form over an existing part.
This process makes “Shell” type parts that can have many uses. Some examples are:
Candy Molds, Toys, Model car bodies, Model airplane parts, Boat hulls, Signs, Holiday decorations, Soap and Candy molds, Containers and packaging.
Chapter 2 - Heat Sources
Most plastics require between 250 and 400 degrees F. to get soft enough. We are not trying to melt the plastic, just make it soft like a sheet of rubber. Your kitchen oven was designed to heat food at these temperatures, so its a safe and convenient way to heat plastic as well. This chapter shows the differences between gas and electric ovens and how to use them effectively.
Find out why heat guns and heat lamps should be avoided. Other heat sources are discussed, such as, electric frying pans and griddles, toaster ovens, hot plates etc.., with advice on using each one.
Chapter 3 - Vacuum Sources
A simple explanation of what vacuum is and how its measured, with charts and conversion tables. Vacuum is commonly rated in “Inches of Mercury” (IN. HG.) Most commercial vacuum forming is done with 25 -27 IN.HG. with a maximum of about 30 inches possible.
Note: Vacuum cleaners only pull 4 to 6 IN.HG. out of a possible 30 IN.HG. Don’t be fooled by the commercials that show them picking up bowling balls. It doesn’t matter how many horsepower, or how loud it is, or how much it dims the lights. Even the best “Shop Vacs” don’t pull very hard, they just flow a lot of air!
This is barely enough to form thin plastic sheets with marginal definition. Learn how to increase that 50% by coupling two vacuum cleaners together. Seven other low cost sources of higher vacuum are discussed, such as. intake manifold vacuum (from your car), Modified bicycle pumps, air powered and electric pumps. Learn how to modify a bicycle pump to pull 27 IN.HG. and use stored vacuum form tanks.
Learn how to get 5 times more forming power by combining a vacuum cleaner with another higher vacuum source to create a “two Stage” system. You won’t find this information available anywhere else!
Chapter 4 - Forming Equipment
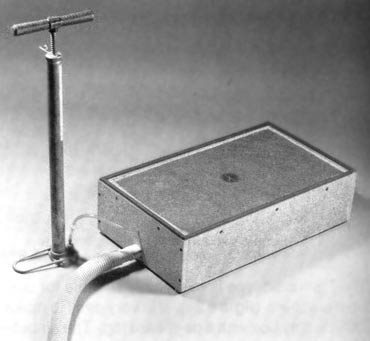
Learn how to make a simple holding frame out of aluminum angle from the hardware store, and use this frame with inexpensive spring clips to hold a plastic sheet for heating. See ideas for simple vacuum boxes made from cake pans, and more sophisticated two stage vacuum boxes.
learn how to modify a sump pump check valve from the hardware store to combine a vacuum cleaner with a second higher vacuum source. This method uses the speed of a vacuum cleaner, but finishes off with a more powerful vacuum source. The valve is easy to make and works automatically.
Chapter 5 - Plastics
There are a million types of plastic sheets, but only a half dozen that you are likely to come across. This chapter discusses the common types and gives you practical advice on choosing a plastic for your application. Properties such as impact resistance, forming characteristics, pre-drying, and cost are considered. Useful tips on where to buy plastic sheets and how to deal with plastic distributors.
Chapter 6 - Molds
The theme of this book is “low budget”, so this chapter focuses mainly on wood and plaster molds. Learn six “common sense” rules of mold making, such as avoiding undercuts, surface preparation and the use of release agents. Read important information on using hollow molds and forming over existing objects. An example shows how to cast a plaster mold to reproduce an existing model car body.
Chapter 7 - Forming
Once you have the equipment built, this chapter gives you practical advice on the actual forming process. Learn how to tell when the plastic is ready to form and learn about common problems and how to solve them. Photographs show sample parts made with different plastics.
A detailed example is given that shows how to form a radio controlled model car body over the plaster pattern created in the last chapter.
Chapter 8 - Finishing
Learn three ways to trim out the finished part depending on thickness. Read about glues and paints for different plastics.
Note: The back of the book contains a supplement with more forming tips and solutions to common problems, as well as information on plans that are available for building your own machines with built in ovens.